Trendaavat aiheet
#
Bonk Eco continues to show strength amid $USELESS rally
#
Pump.fun to raise $1B token sale, traders speculating on airdrop
#
Boop.Fun leading the way with a new launchpad on Solana.
Before & After: How we strengthen 3D-printed parts for flight.
When we 3D print High-Pressure Turbine (HPT) vanes for our Symphony engine, what you don’t see is just as important as what you do.
Before: Fresh off the printer, parts can contain microscopic voids (tiny flaws that act like stress magnets). They also hold onto residual stresses from the printing process itself.
After: We use Hot Isostatic Pressing (HIP) to apply 2,100°F and 25,000 psi for 4 hours, collapsing internal voids and densifying the part. Then, we apply Heat Treatment (HT): 2,300°F for 2 hours, followed by rapid cooling at a rate of 230°F per minute. This relieves internal stress and toughens the metal.
The result? Stronger, more stable, flight-ready vanes.
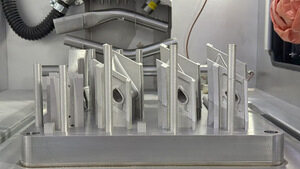
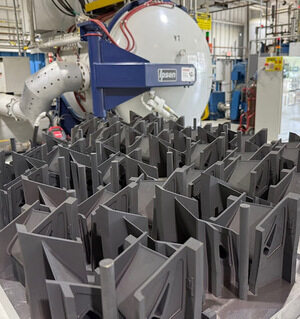
18,86K
Johtavat
Rankkaus
Suosikit